– Polska ma rozwinięte zdolności w pewnych obszarach, w innych czeka ją dużo pracy. Przykładem mocnych stron polskiego przemysłu jest produkcja luf w Hucie Stalowa Wola, gdzie transfer technologii do tych zakładów jest obecnie relatywnie prosty. […] Przykładem pięty achillesowej sektora, w dziedzinie produkcji czołgów, są silnik czy elementy układu napędowego – mówi Jerzy Aleksandrowicz ekspert ds. obronności Fundacji im. Kazimierza Pułaskiego w rozmowie z BiznesAlert.pl.
- – Transfer technologii dotyczy wielu, nawet setek elementów. To nie jest tylko montowanie dostarczonych części w gotowy system. To stopniowa produkcja na terenie Polski coraz większej części podzespołów, które można uzasadnić z ekonomicznego punktu widzenia – wyjaśnia Jerzy Aleksandrowicz.
- – Polska uzyskała szeroki transfer technologii od brytyjskiego MBDA, który podszedł do sprawy bardzo partnersko. Pokazuje to, że zagraniczni producenci są bardzo otwarci na współpracę. Dzięki temu polski przemysł może mieć szansę zachowania konkurencyjności na rynku europejskim – mówi rozmówca BiznesAlert.pl
- – Umiejscowienie zakładów w dużych miastach, jak na przykład Poznaniu, sprawia, że rywalizacja o pracownika jest bardzo duża. Zwłaszcza wykwalifikowanego. Zlokalizowanie ich blisko wschodniej granicy sprawia, że będą narażone w przypadku agresji. Jednak najwyższe bezrobocie jest w województwach położonych na wschodniej ścianie Polski, co sprawia, że łatwiej tam pozyskać pracownika – wyjaśnia problematykę Aleksandrowicz.
BiznesAlert.pl: Jak wygląda kwestia transferu technologii przy umowach zbrojeniowych? Może zacznijmy od tego czy jest to jakoś uregulowane? Na jakich polskich przepisach opiera się transfer technologii?
Jerzy Aleksandrowicz: Transfer technologii zdarza się relatywnie często przy umowach zbrojeniowych. Jest to tendencja światowa. Są kraje takie jak Rumunia, które ze względu na koszty transferu technologii jasno wskazują, że rezygnują z niego żeby obniżyć koszt zakupu. Albo kraje takie jak Japonia, które nie licza się z kosztami i wymagają dużego zakresu transferu jednak skutkuje to tym, że jednostkowy koszt egzemplarza uzbrojenia jest horrendalny, o kilkadziesiąt czy nawet 100 procent często wyższy niż w innych krajach.
Ale czym właściwie jest transfer technologii?
To, może zacznijmy od przepisów. Bez zanudzania szczegółami, to przez długi czas transfer technologii opierał się głównie na przepisach ustawy offsetowej. Tutaj trzeba przypomnieć czym jest offset – to narzędzie służące kompensacji wydatków ponoszonych przez kraj dokonujący zagranicą zakupów uzbrojenia. To przykład offsetu na F16 w Polsce i bardzo często taka kompensacja nie dotyczyła przemysłu zbrojeniowego. Offset w takiej formie został jednak zakazany w Unii Europejskiej, między innymi dlatego, że uznano go za narzędzie zaburzające wspólny rynek. W momencie, gdy transfer technologii wojskowej został mocno ograniczony przez Unię Europejską, powstały rozwiązania quasi-offsetowe. Zostały one skonstruowane tak, by nie narażać się na spory z Komisją Europejską. Co ciekawe, stosują je dość powszechnie „stare kraje wspólnoty”. Ostatnim dużym przetargiem, który miał uwzględniać szeroki transfer technologii w ramach offsetu, była umowa na Caracale. To była taka hybryda starych i nowych przepisów. Jednak pomimo trudnej sytuacji prawnej, udało się zapewnić doskonałe warunki transferu technologii bezpośrednio związanej z zamówieniem. Niestety zostało to później zmarnowane, bo postawiono całkowicie nierealne, nowe wymagania, a tak się nie powinno postępować z partnerami. Obecnie realizowane programy są trochę inne, bazują na zawartych umowach między rządami, na przykład Republiki Korei i Polski (programy K2 i K9), USA i Polski (program Wisła), czy Wielkiej Brytanii i Polski (programy Narew i Miecznik). Przy umowach amerykańskich nadal obowiązują często sztywne i mało dostosowane do potrzeb wymagania, jednak związane już ze zbrojeniówką. Natomiast w umowach z Wielka Brytanią i Koreą to głownie na podstawie umów bilateralnych przemysł dostaje swobodę negocjowania transferu technologii. Jego ramy są określane przez wojsko, na bazie ich potrzeb, a także rachunku ekonomicznego przedsiębiorstw. To dużo bardziej skuteczne rozwiązanie, dające większe pole do osiągnięcia sukcesu, jednak wymaga też niewspółmiernie większego zaangażowania krajowego przemysłu, większej kultury organizacyjnej i planowania wieloletniego.
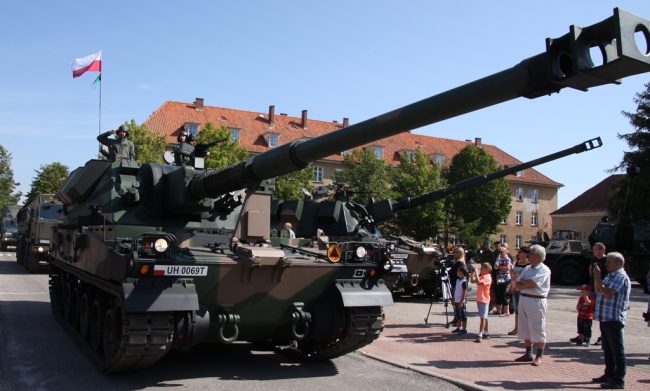
Częścią umowy między Koreą, a Polską, jest kwestia transferu technologii. Co tutaj dokładnie kryje się pod tym terminem?
Koreański przemysł wydaje się bardziej otwarty na transfer technologii niż partnerzy z USA czy Niemiec. Tutaj tylko Brytyjczycy i kiedyś Izrael były tak otwarte na współpracę. W sumie jeszcze Norwegia zaoferowała nam dobre warunki. Ale wracając do pytania to może na przykładzie czołgu K2 możemy zauważyć, że strona koreańska od samego początku zakładała, iż polski przemysł będzie jednym z kluczowych podmiotów mających na celu realizację umowy. Koreańczycy proponowali różne modele współpracy, począwszy od ścisłego partnerstwa jak joint venture, kooperację opartą na umowach podwykonawczych, czy konsorcjum. I wydaje się, że to ostatnie rozwiązanie było preferowane przez polską stronę. Hyundai Rotem, jako producent czołgu oświadczał publicznie chęć współpracy z polskimi spółkami państwowymi, czyli z Polską Grupą Zbrojeniową, ale zgodnie z deklaracjami spółki nie wykluczała w przyszłości współpracy z rynkiem prywatnym, gdzie już dziś nawiązano relacje z grupą WB przy okazji prac na czołgami w wersji GF. Przykładem takiej otwartości są też wizyty, które przedstawiciele koreańskiej firmy odbywali na polskich uczelniach. Oceniając całokształt to uważam, że w końcu, po raz pierwszy od 1989 roku, jest realna szansa na zbudowanie polskiego czołgu.
Do tej pory, w zakresie technologii czołgowych, polski przemysł współpracował z niemieckim. Mam na myśli czołgi Leopard. Modernizacja Leoparda 2 idzie jednak bardzo powoli. Powoduje to zrozumiałe niezadowolenie nie tylko przemysłu, ale i sił zbrojnych, którym zależy na zachowaniu tempa dostaw i wysokiej zdolności operacyjnej sprzętu wojskowego.
Jak wyglądają zdolności polskiego przemysłu do produkcji nowoczesnego sprzętu, na przykład czołgów albo armatohaubic?
Polska ma rozwinięte zdolności w pewnych obszarach, w innych czeka ją dużo pracy. Przykładem mocnych stron polskiego przemysłu jest produkcja luf w Hucie Stalowa Wola, gdzie transfer technologii do tych zakładów jest obecnie relatywnie prosty. Przy produkcji haubic KRAB polski przemysł w sposób niemal perfekcyjny rozwinął te zdolności, tym samym absorpcja nowych technologii, nie wymaga dużych zmian niosących za sobą znaczne koszty i względnie możliwy jest szybki czas absorbcji. Przykładem pięty achillesowej sektora, w dziedzinie produkcji czołgów, są silnik czy elementy układu napędowego. Więc, KRAB to przykład tego jak historycznie umieliśmy krajowo zintegrować na przestrzeni kilkunastu lat dość skomplikowane technologie i je rozwinąć. Oby był to przykład zawsze powtarzany.
Transfer technologii dotyczy wielu, nawet setek elementów. To nie jest tylko montowanie dostarczonych części w gotowy system. To stopniowa produkcja na terenie Polski coraz większej cześć podzespołów, które można uzasadnić z ekonomicznego punktu widzenia. Co więcej, bazując na ogólnodostępnych deklaracjach, Korea jest otwarta na współpracę przy modernizacji produktu, a docelowo stworzenia tego co Koreańczycy nazywają czołgiem przyszłości, a w polskiej przestrzeni medialnej jest określane jako K3.
Wspominał Pan o konieczności odbudowy niektórych ze zdolności polskiego przemysłu zbrojeniowego. Ile może potrwać taki proces w kontekście produkcji zaawansowanego uzbrojenia?
Ponownie można wrócić do udanego transferu technologii z Wielkiej Brytanii i Korei. Mało już kto pamięta, że to nieistniejąca już niestety firma Samsung Techwin była odpowiedzialna za ustanowienie zdolności do produkcji podwozi do Kraba. W ramach Kraba otrzymaliśmy też transfer technologii z Wielkiej Brytanii, dotyczący wieży AS90. Więc rodzicami Kraba były właśnie przemysły koreański i brytyjski.
Podkreślę jeszcze raz, bo trzeba o tym pamiętać w dobie krytyki transferów technologii przez część komentatorów, że właśnie ten przykład pokazuje, że umiemy ustanawiać w kraju zdolności dość sprawnie i tutaj optymizmem napawa fakt, iż prezesem PGZ została osoba mająca takie właśnie doświadczenie.
Odbudowa zdolności oznacza często de facto ich budowę od początku. Ciężko dokładnie powiedzieć, ile taki proces może potrwać, bo jest to proces skomplikowany, gdzie wiele zależy od pierwszych kroków, które zostaną podjęte przy pozyskaniu technologii. Polski przemysł w pierwszej kolejności dostanie propozycję prac nad elementami, które go najbardziej interesują. Przy czołgu K2 zostały one zidentyfikowane i wybrane przy udziale spółek z grupy PGZ. Można powiedzieć, że wprowadzenie polskich elementów jest perspektywą co najmniej kilku lat.
W przypadku elementów napędowych, to niestety, ale Polska sama pozbawiła się takich zdolności likwidując zakład PZL Wola. Przez to obecnie nie może realizować samodzielnych prac nad silnikami. W kraju znajdują się co prawda działające fabryki firm zagranicznych produkujące silniki jak na przykład Mercedes, są one jednak przeznaczone na rynek cywilny. To silniki, które nie nadają się do wszystkich pojazdów wojskowych, dlatego do haubic czy czołgów musimy te silniki obecnie kupować za granicą.
Generalnie ze względu na słabość w obszarze krajowej produkcji silników ze smutkiem należy odnotować decyzję grupy Stellantis, która przeprowadza proces wygaszania produkcji w zakładzie spółki FCA Powertrain w Bielsku-Białej. Szkoda, że nie skorzystano z okazji i PGZ nie kupił tych zakładów.
Czy w obecnie dostarczanych czołgach są zastosowane jakiekolwiek polskie rozwiązania, czy są to wersje identyczne, jak te użytkowane przez Siły Zbrojne w Korei? Czy w przyszłości możemy się spodziewać szerokiego transferu technologii i szerokiej współpracy pomiędzy przemysłem polskim i koreańskim?
Można mówić o wielu aspektach. Przykładowo, na podstawie współpracy z WB Electronics strona koreańska pozyskuje środki łączności do wersji Gap Filler, czyli do jeszcze niespolonizowanej a już dostarczanej do SZ RP. Udział polskiego przemysłu będzie coraz bardziej istotny – musimy pamiętać, że transfer technologii to proces, w ramach którego zdolności będą pozyskiwane stopniowo, a więc i udział komponentów produkowanych w Polsce będzie rósł stopniowo. Ale stronę koreańska, interesuje tez pozyskanie elementów opracowanych w Polsce. To powinna być naszą ambicja aby dokonać tez polonizacji czołgów armii Republiki Korei.
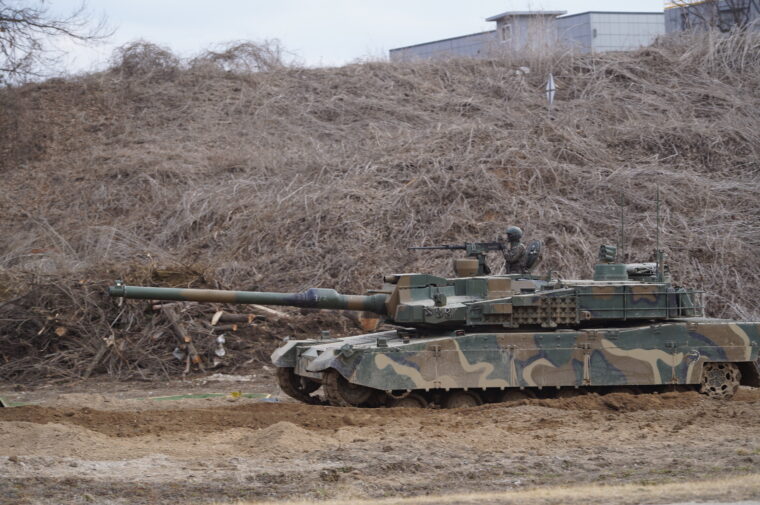
Polski przemysł zbrojeniowy pozyskuje technologie nie tylko z Korei. Jakie są przykłady korzystnego transferu?
Przede wszystkim należy wskazać program Narew. Polska uzyska szeroki transfer technologii od brytyjskiego MBDA w zakresie wyrzutni i efektorów. Pokazuje to, że zagraniczni producenci są bardzo otwarci na współpracę. Dzięki temu polski przemysł może mieć szansę zachowania konkurencyjności na rynku europejskim. Innymi przykładami, realizowanymi lub będącymi w trakcie negocjacji, jest program okrętów obrony wybrzeża typu Miecznik czy program Kruk, dotyczący pozyskania śmigłowców uderzeniowych. Ten ostatni opiera się na trochę innych zasadach, czyli jest realizowany w oparciu o ustawę offsetową. W jego ramach będą transferowane zdolności, ale w ograniczonym zakresie, głównie serwisowania. Należy jednak pamiętać, że koszty eksploatacji w cyklu życia produktu stanowią nawet 50-70% kosztów całkowitych użytkowania systemu uzbrojenia. Więc przy śmigłowcach to bardzo ważny transfer technologii.
Wspomniany czołg K2 i program Narew będą transferami najpełniejszymi, przynajmniej w teorii, jeżeli chodzi o zakres przekazania technologii. Pozwolą na zbudowanie krajowych pełnych zdolności. Nie tak jak przy Rosomaku, który nie dał zdolności potrzebnych do opracowania pojazdu krajowego, bo umowy wiązały nas bardzo niekorzystnie.
Warto w tym miejscu przypomnieć historię już zrealizowanych, udanych transferów technologii. Należy wspomnieć również o Morskiej Jednostce Rakietowej, która została pozyskana od norweskiego Kongsberga – tutaj polskie spółki pozyskały szerokie kompetencje w zakresie serwisu, a nawet opracowywały samodzielnie część komponentów. Doświadczyliśmy też udanego transferu technologii od Harrisa w zakresie systemów łączności. W zakresie produkcji amunicji, z pełnym sukcesem odbywa się produkcja pocisków Spike w MESKO.
Jakie wyzwania stoją przed sprowadzeniem technologii do Polski?
Dużym problemem jest brak modernizacji i rozwoju polskiego przemysłu. Przykładowo, do niedawna Polska bazowała na liniach produkcyjnych amunicji zawierających rozwiązania z lat 20-tych ubiegłego wieku. Obecnie potrzebne są inwestycje w tym zakresie, i to stałe. W pewnym momencie w Polsce zabrakło spojrzenie perspektywicznego. Cała Europa dała się oszukać wizją tego, że nigdy więcej bezpośrednio nie doświadczy wojny. Trzeba zaznaczyć, że nie tylko Polska ma problemy produkcyjne, a mają je wszystkie kraje NATO.
Oprócz stabilności finansowania, polski przemysł zbrojeniowy musi lepiej wydawać środki. Obecnie sektor wydaje fundusze w sposób skuteczny, ale niekoniecznie optymalny.
Wojsko powinno też zagwarantować odpowiedni wolumen zamówień, aby w ramach konkretnych programów przemysł mógł realizować niezbędne inwestycje. Kolejnym aspektem są zasoby ludzkie. Trzeba nie tylko je znaleźć, ale i przeszkolić oraz utrzymać pracowników. Skłonić do tego by skuszeni wyższym wynagrodzeniem nie wybrali konkurencji. Łączy się to z kolejnym wyzwaniem, jakim jest właściwa lokalizacja zakładów. Umiejscowienie zakładów w dużych miastach, jak na przykład Poznaniu, sprawia, że rywalizacja o pracownika jest bardzo duża. Zwłaszcza wykwalifikowanego. Zlokalizowanie ich blisko wschodniej granicy sprawia, że będą narażone w przypadku agresji. Jednak najwyższe bezrobocie jest w województwach położonych na wschodniej ścianie Polski, co sprawia, że łatwiej tam pozyskać pracownika.
Bardziej szansą niż wyzwaniem jest współpraca przemysł-nauka. To ośrodki akademickie kształcą przyszłe kadry, jest to długi proces, o który należy szczególnie zadbać. Jeżeli zagraniczne firmy lokują produkcje w Polsce też powinny o to zadbać. I to już się dzieje, coraz więcej zagranicznych firm współpracuje z polskimi uczelniami technicznymi. Takie złożone projekty jak Narew, Miecznik czy Wisła pokazały też, że trzeba szkolić nie tylko inżynierów, ale i techników p.. spawaczy, tokarzy czy ślusarzy. Dynamiczne zmiany edukacyjne w ubiegłych latach i atrakcyjniejsze zarobki za granicą sprawiły, że w Polsce jest mało techników. Innymi przykładami dbania o przyszłego pracownika jest dialog producentów z jednostkami samorządu terytorialnego w celu odtworzenia lub podniesienia jakości kształcenia technicznego – zaoferowania nowych kierunków w istniejących technikach, czy dofinansowania już realizowanych kierunków kształcenia.
To jeszcze pytanie, czy transfer technologii się opłaca? Bo podnosi przecież koszt zakupu sprzętu.
Tak, oczywiście. Dlatego to słuszne pytanie bo zapomina się o tym. Transfer kosztuje. Wrócę do przykładu transportera opancerzonego. Pomimo problemów z biznesowego punktu widzenia, tj. ograniczeń eksportowych, to ze względów produkcyjnych za udany transfer technologii należy uznać nasze Rosomaki. Pozwoliło to na ich serwisowanie. Ponadto mimo upływu czasu nadal pojazdy te są cenione przez naszych żołnierzy, a Rosomak S.A. uzyskało pewne kompetencje. Jednak z punktu widzenia biznesowego, to nie był to sukces eksportowy bo jak wiele razy płynęły sygnały z PGZ, nie było swobody na eksport do innych państw.
Czy możemy produkować wszystko? Tak możemy, tylko będzie to bardzo drogie. A wojna to też ekonomii bojeśli będziemy strzelać z czegoś co jest relatywnie drogie do systemów które są tanie, to może się okazać, że nasze drogie elementy uzbrojenia skończą się, bo mamy ich mniej niż gdyby zostały pozyskane w bardziej przystępnej cenie, bezpośrednio od producenta. Z tym boryka się Ukraina.
Pozyskiwanie technologii jest na ogół czasochłonne i kosztowne, proces ten bowiem to nie tylko pieniądze, ale również inwestycje w infrastrukturę, zakup linii, reorganizacja zakładu, zmiana kultury organizacyjnej, nauka techników, zmiany dotyczące technologii materiałowych i wiele innych.
Transfer technologii to też wyzwanie dla strony przekazującej, ponieważ to na niej spoczywa odpowiedzialność za produkt, nad którym nie do końca ma pełną kontrolę. W skomplikowanym procesie projektowania i produkcji transferujący przecież musi uwzględnić podmioty, które mają za zadanie podjąć to wyzwanie i dostarczyć finalny produkt zamawiającemu. Musimy też pamiętać o wyzwaniach związanych z różnicami kulturowymi, barierami językowymi czy organizacyjnymi strony przekazującej i odbierającej transfer technologii. Jest wiele czynników, które muszą współgrać ze sobą a jeszcze więcej wymagających stałego wysiłku w celu zabezpieczenia właściwego jakościowo transferu. .
W idealnym świecie, każda technologia powinna być oparta o własne zdolności. Należy jednak pamiętać, że są miejsca, w których dogonienie czołówki własnym wysiłkiem i na własny koszt może zająć bardzo dużo czasu, a transfer technologii może ten proces po prostu przyspieszyć.
Rozmawiał Marcin Karwowski
Wolski: Francuskie atomówki mogą ochronić Europę, jeżeli będzie problem z USA w NATO (ROZMOWA)